The leading crane automation. Efficient. Safe. Sustainable.
Cranium optimizes operating processes, reduces risks and increases productivity. With intelligent control, collision detection and sustainable solutions, we are creating the future of crane automation.
Without automation, your crane operation remains unsafe, inefficient and expensive.
Your daily crane work involves high risks of accidents
Your crane operators work in demanding conditions, which increases their workload and the risk of accidents.
Differences in expertise influence your efficiency
The efficiency of your crane work depends heavily on the experience of individual operators, which leads to variations in productivity.
A lack of precision slows down your processes
Your crane operators often need several attempts to precisely control heavy or sensitive loads. That costs time.
Maximum protection and reliable operation
Your right hand in crane operation
Cranium offers a variety of driver assistance systems that reduce the risk of accidents and create more attractive working environments for new or inexperienced crane operators.
Full control over the status of your crane - in real time and precisely
Cranium provides time series logging for internal and external processes without time limits. Maintain an overview of driving behavior and causes of accidents.
Proven in practice, built for the future
Developed for the highest demands, Cranium impresses with its high stability and reliability – tested in the most demanding scenarios for uncompromising performance.
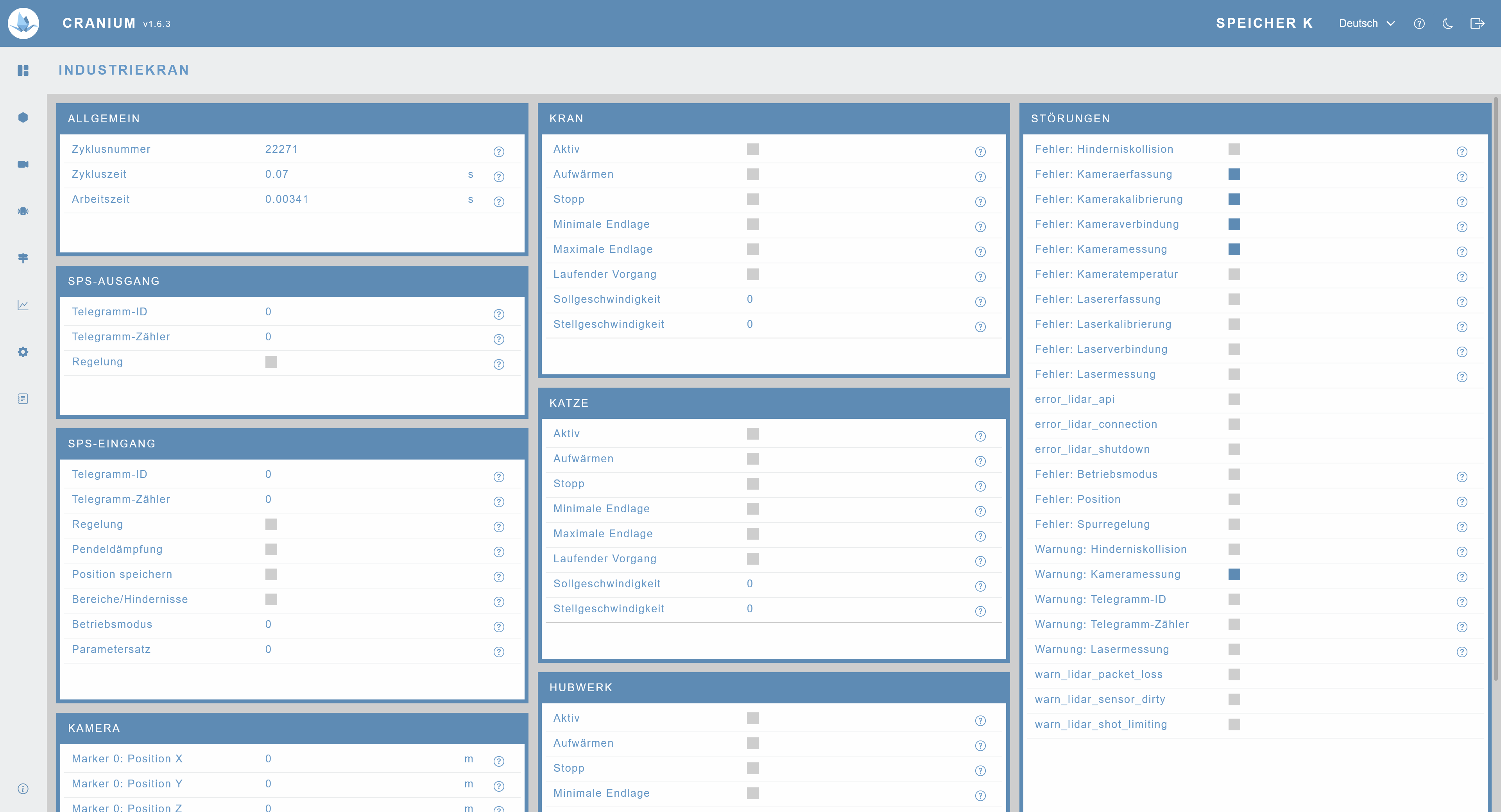
Protect your crane operation now
Contact us directly and let us work together to find the ideal solution for your business.
Our solution, as versatile as your business
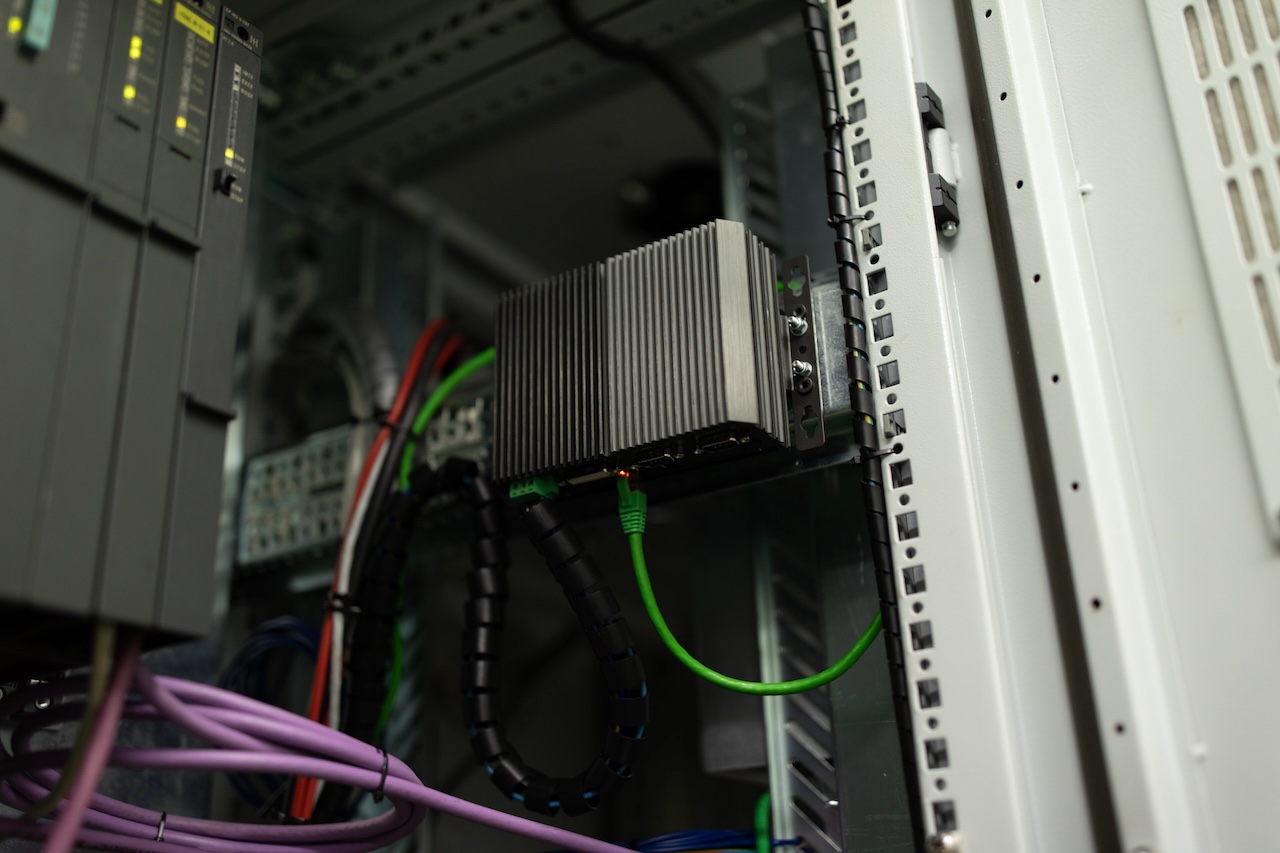
As flexible as your system requires
Each Cranium module can be licensed as required. You can also add further modules at a later date while the system is already running.
The interface to existing systems
Cranium has various interfaces for integration into your PLC. For gantry cranes, we also offer you the connection to TOS, CIDS/OCR, FCMS or SACS. Here we rely on customized solutions.
Always stay up to date
We always offer you reliable firmware and software updates for your Cranium system. This means that you can use all subsequently licensed functional enhancements on your product without any problems.
Discover the wide range of possibilities now
Contact us directly and let us work together to find the ideal solution for your business.
Intuitive web interface included
Flexibly manage your crane configurations
The Cranium interface allows you to duplicate your crane configurations. By importing and exporting, we make commissioning easier and at the same time offer you a simple backup solution.
Graphically define obstacles and routes
Our interface makes it easy to define paths and areas for your crane. You determine which position your crane can move to and which paths it can take to reach it.
Step-by-step guided commissioning
The Cranium interface enables guided commissioning. All necessary configurations are explained here and can be adjusted accordingly.
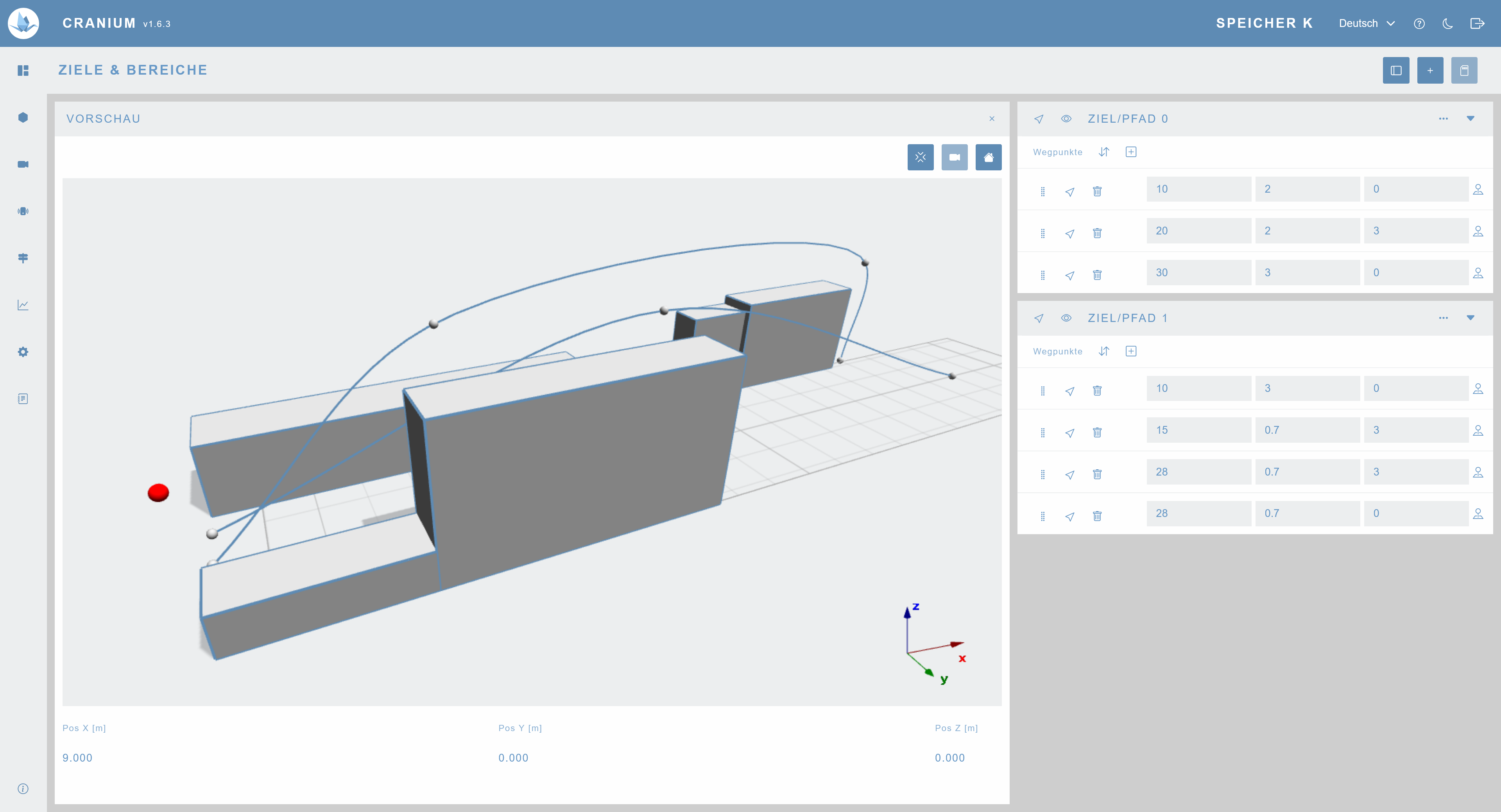
Enjoy ease of use that makes your everyday life easier
Contact us directly and let us work together to find the ideal solution for your business.
Reliable service for your cranes
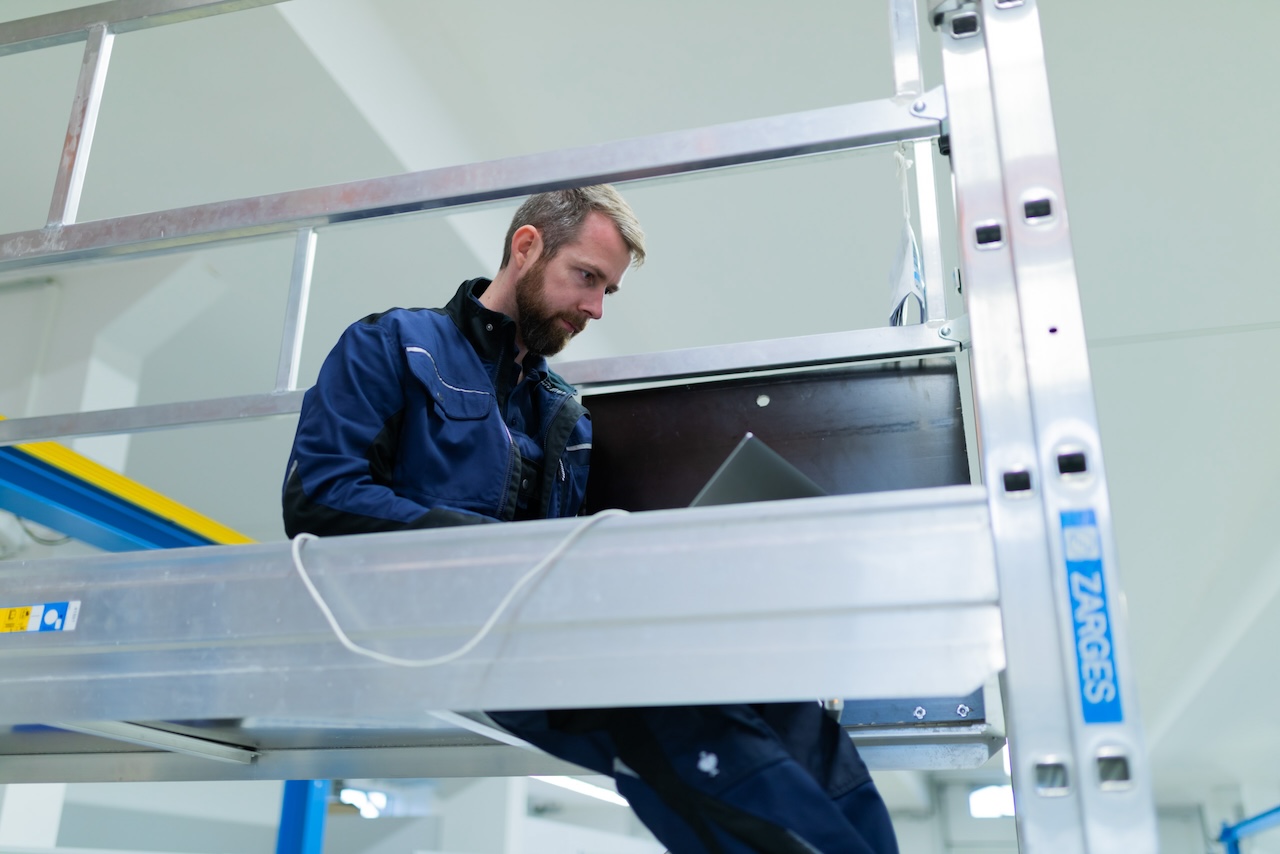
Go easy on the crane and load
With Cranium, you can optimize the braking and acceleration ramps of your crane and benefit from soft landing for suspended loads, among other advantages.
Availability that lasts
All supplied, conductive components are selected with a view to their long-term availability. This means that all components can be easily replaced for at least 10 years.
We guarantee satisfaction
We do everything we can to meet your expectations. We always find solution-oriented and fair ways to work together on an equal basis.
Increase the lifespan of your systems now
Contact us directly and let us work together to find the ideal solution for your business.
Ready for use wherever efficiency counts
Cranium for gantry cranes
Optimize the operation of your gantry cranes with innovative automation solutions. Precise control, fast turnaround times and maximum safety – for maximum efficiency and sustainability in your port operations.
Cranium for Industrial Cranes
Increase the performance of your overhead cranes with modern automation solutions. Precise control, greater efficiency and maximum safety – perfect for every environment and every requirement.
Cranium for Intermodal Cranes
Optimize your intermodal operations with intelligent automation solutions. Efficient control, fast turnaround times and seamless processes – for maximum performance in terminal operations.
Your success starts with the right components
Your Contacts
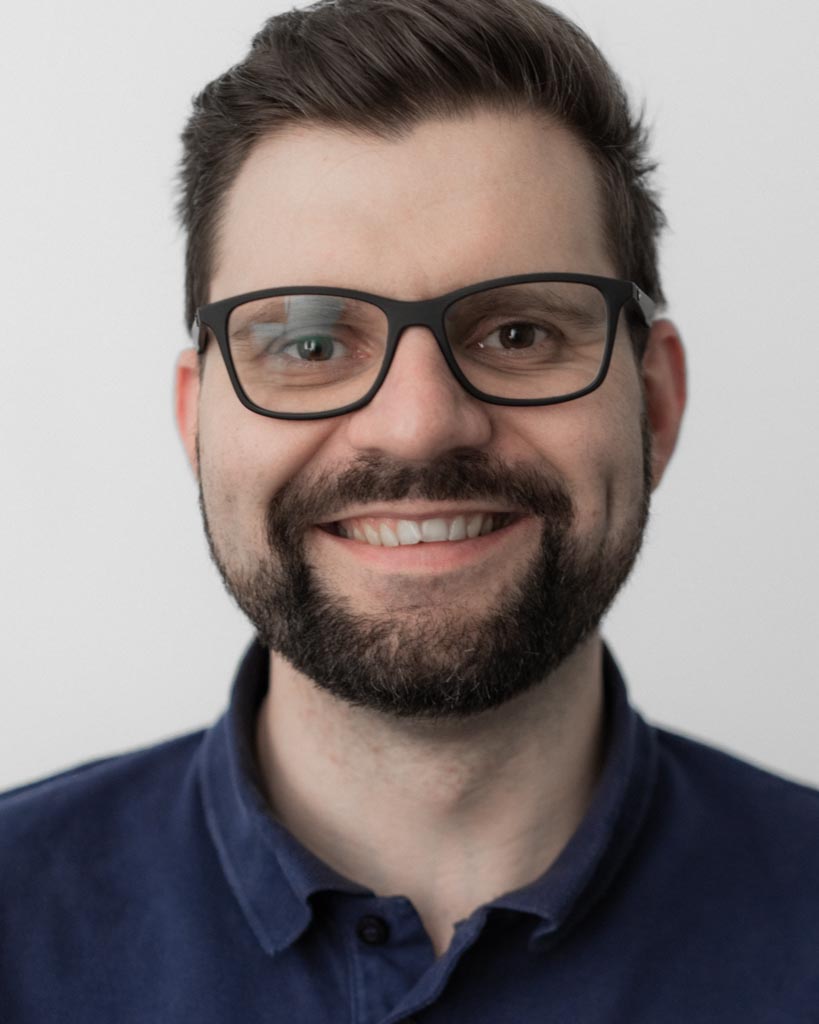
Martin Kirst
Chief Executive Officer
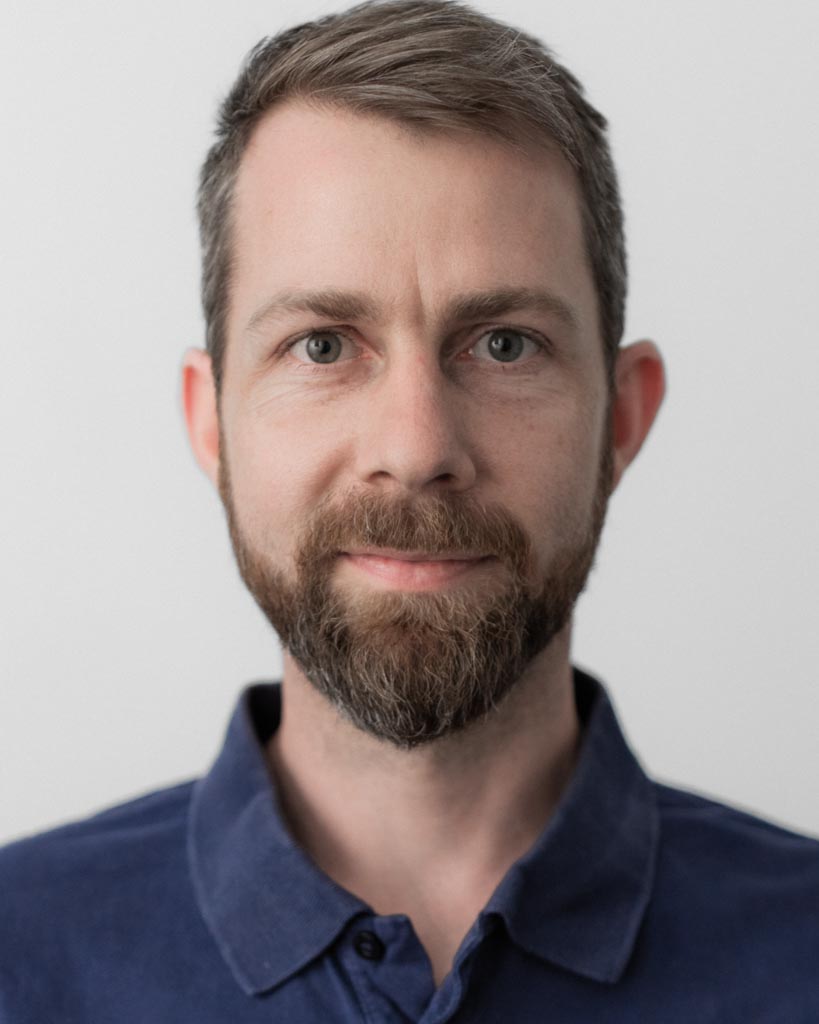
Richard Herrmann
Head of Engineering
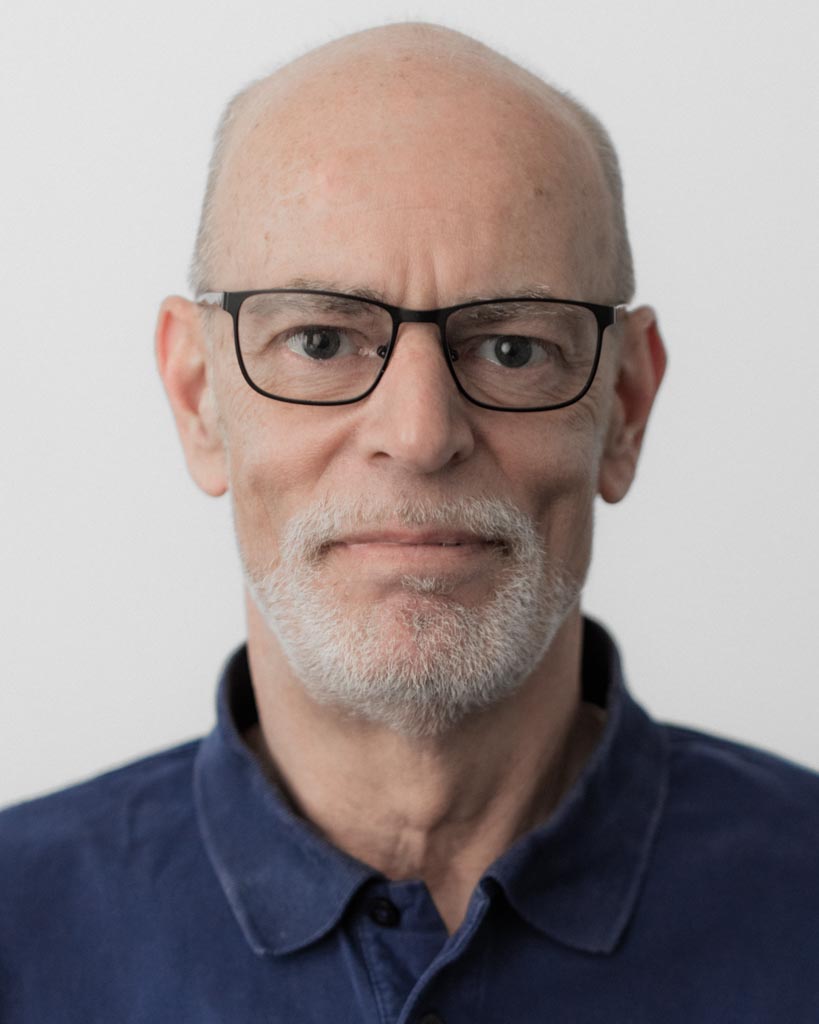
Uwe Ochs
Sales Account Manager
Any Questions?
Please use the contact form below. We will be happy to answer your questions about Cranium. You can also reach us by phone at +49 391 74478204 (Mon-Fri 9:00 am – 06:00 pm).